Titanium and titanium alloy ingots and standardization
The production of titanium and titanium alloy ingots in China started in the 1950s. In 1964, the industrial production of titanium processed materials was realized. With the popularity of titanium characteristics, titanium has the advantages of high specific strength, corrosion resistance, non-magnetic properties, low damping, high and low temperature performance, good compatibility with carbon composites, and good biocompatibility. Fully explored and applied, it has been hailed as "space metal" and "marine metal", and has been widely used in aerospace, shipbuilding, marine engineering, chemical, electric power, metallurgy, medical, sports and leisure industries. Therefore, the demand for titanium in the world is increasing year by year, especially in the past 10 years after entering the 21st century, the growth rate is faster. Therefore, the use of titanium will also become one of the important indicators of a country's comprehensive strength. However, due to the particularity of titanium and titanium alloy ingot production equipment and the difficulty in mastering its compositional uniformity control technology, as well as equipment capabilities and other factors, the choice to purchase finished ingots is the best decision for some titanium processing enterprises to solve raw materials. In 2009, China's titanium ingot production capacity has reached 82,900 tons / year [1], the actual production of titanium ingots 41,164 tons [1]. The abundant production capacity not only satisfies the demand for domestically produced titanium processed materials, but also greatly improves the export situation of titanium ingots due to the low price of domestic titanium ingots. Only Baoji Titanium Industry Co., Ltd. has exported more than 2,100 tons of titanium ingots since 2004.
Due to the long-standing national and industry standards for titanium and titanium alloy ingots in China, some companies have established corporate standards or signed technical documents with users for the convenience of trading. These technical documents have promoted titanium ingots for a period of time. transaction. No special standards have been found in foreign countries. At present, the technical requirements for exporting titanium ingots mainly adopt user's enterprise standards, such as Boeing's corporate standards, Japan Advanced Materials Corporation's corporate standards, and Baoji Titanium Industry Co., Ltd. corporate standards. In this context, Baoti Titanium Co., Ltd. and Baoji Titanium Industry Co., Ltd. proposed the approval of the National Standards Committee in 2007 to prepare the National Standard for Titanium and Titanium Alloy Ingots, which was officially released in January 2011. The standard number is GB/T 26060-2010, which was implemented on October 1, 2011.
2 Status of titanium and titanium alloy ingots
2.1 Technical status
As we all know, titanium has strong chemical activity,
The high melting point and the impurity content of the gap are extremely sensitive to the influence of its properties, which promotes the smelting of titanium and titanium alloy ingots under vacuum or inert atmosphere, so the chemical composition and composition uniformity of titanium and titanium alloy ingots are controlled. Technologies such as metallurgical quality control place high demands. At present, the technology is only available to the United States (Timet, RTI, etc.), Japan (Kobe Steel, Sumitomo, Toho, etc.), Russia (Vsmpo and other companies), China and other countries and companies. In particular, the compositional uniformity control technology of titanium alloy ingots and large-size ingots is one of the important bottlenecks for the production of special-purpose and large-size, high-quality titanium and titanium alloy products.
Since the United States, Japan, Russia and other countries have started industrial research on the production of titanium and titanium alloy ingots since the early part of the last century, they have accumulated rich experience and mastered the smelting technology of titanium and titanium alloy ingots earlier than domestic.
Domestic general-purpose small and medium-sized titanium and titanium alloy ingot smelting technology has matured, medium-sized and above enterprises have basically mastered, and small enterprises need to be improved. Important applications of titanium alloy ingots and large-scale titanium and titanium alloy ingot smelting technology only a few companies such as Baoji Titanium Industry Co., Ltd. master the core technology. 2.2 Status of domestic production
The production capacity and output of China's titanium and titanium alloy ingots were given from 2005 to 2009. As can be seen from Figure 1, the output of ingots increased from 16,230 tons in 2005 to 41,164 tons in 2009, which is 2.54 times that of 2005; the production capacity increased from 33,800 tons in 2005 to 82,900 tons in 2009, which is 2005. 2.45 times the year.
From 2005 to 2009, the annual production capacity surplus was 17,570 tons, 18,480 tons, 13.831 tons, 29,492 tons and 41,736 tons, and the percentage of surplus capacity in total capacity was 52%, 46%, 29%, 43%. And 50%. It is not difficult to see that from 2005 to 2007, the surplus of production capacity showed a downward trend, and the surplus of production capacity after 2007 showed an expanding trend. It shows that after 2007, the production of equipment and the amount of equipment already in operation of various production enterprises have expanded.
3 Standardization of titanium and titanium alloy ingots
Although China has been producing titanium and titanium alloys since the 1960s, there have been no national, industry or local standards for titanium and titanium alloy ingots for nearly half a century. In the actual production transaction process, the enterprise standard is mainly used or the technical requirements are determined by negotiation between the supplier and the buyer. The main reason for this phenomenon is due to the long-term production and use of titanium and titanium alloys in China. In the late 1990s, with the advancement of technology and the increasing awareness of titanium and titanium alloy products in various industries, especially in the past 10 years, the demand for titanium products in various international and domestic industries has expanded, which has jointly promoted the rapid growth of the domestic titanium industry. development of. Titanium production and processing enterprises of all sizes in China have sprung up all over the country and have risen rapidly throughout the country. The incomplete production process has promoted the expansion of trading volume of titanium and titanium alloy ingots.
According to the unified deployment of the National Standardization Administration Committee, and in accordance with the requirements of the “Notification of the National Standards Committee [2007] No. 100 on the fifth batch of national standards revision plan for 2007>, Baoti Titanium Co., Ltd. and Baoji Titanium Co., Ltd. The company drafted the "Titanium and Titanium Alloy Ingot" national standard, project plan number 20079136-T-610, completed preparation and approval in 2008.
This standard is a new standard for the production and processing of titanium and titanium alloys. The main contents and technical indicators are as follows:
3.1 Production equipment
In view of the current status of production equipment in the titanium and titanium alloy ingot industry, the most widely used vacuum consumable electric arc furnace (VAR) and electron beam cold bed furnace (EBCHM furnace) are recommended in this standard.
3.2 Chemical composition of the ingot
At present, the chemical composition control levels of various grades of titanium and titanium alloy ingots specified in the national standard are quite mature. Therefore, the standard stipulates that the grade and chemical composition of titanium and titanium alloy ingots should meet the requirements of GB/T 3620.1. The brand and nominal components specified in GB/T 3620.1 and the corresponding foreign brands are shown in Table 1.
3.3 Ingot diameter (thickness and width) and its allowable deviation
According to the technical requirements of domestic and foreign commercial ingots and the factors affecting the processing volume of ingot casting machine in the actual production process (the main influencing factors are the shrinkage of the ingot itself - the thermal expansion and contraction of the material, the deformation of the ingot, resulting in irregular shape of the ingot, The local deeper defects lead to a large amount of local grinding, etc.), which stipulates the allowable deviation of the diameter (thickness and width) of the ingot.
3.4 Length and single weight of ingot and its allowable deviation
Considering the differences in the production capacity of the production equipment of various domestic manufacturers and the uncertainty of market demand, there is no specific regulation on the length and weight of the ingot and its allowable deviation, which is determined by the supplier and the buyer according to the specific requirements. Indicated in the contract to better adapt to the market and improve the enforceability of the standard.
3.5 Ingot head and chamfer
From the actual production requirements and technical requirements of the current processing materials manufacturing enterprises, as well as the consideration of transportation and storage processes, the standard stipulates that the head of the ingot should be driven to the flash, and the edges and ends of the head and tail should be chamfered and chamfered. The size is specified to be ≥ 20 mm × 40 ° to 50 °.
3.6 Phase change point temperature of ingot
The β-transition point temperature of the ingot has certain guiding significance for the formulation of the ingot casting and subsequent processing. In general, after the composition of the ingot is determined, the temperature range of the β-transition point is basically constant, and can usually be determined by empirical formula, metallographic method or differential thermal method. GJB 3763 has given the names of commonly used titanium and titanium alloys. The temperature of the β transition point, therefore, the standard does not impose a mandatory regulation on the determination of the temperature point. It is only specified as “When the demander requests and is specified in the contract, the titanium alloy ingot should be measured for the β transformation temperature. value".
3.7 Ultrasonic inspection of ingots
The existence of shrinkage holes in ingot casting is inevitable. However, in the production process of processed materials of different product forms, in order to make full use of resources and improve the yield, the defects caused by the casting shrinkage in the ingot casting can be carried out in different processes. Effectively removed. Therefore, the standard does not impose mandatory requirements on the removal of the indentation of the ingot casting, and can be flexibly processed according to the needs of the purchaser. In order to facilitate the control of the casting shrinkage hole in the subsequent process of producing the processed product and to ensure the internal quality of the processed product, the standard proposes ultrasonic inspection of the ingot to determine the distance between the casting shrinkage hole and the ingot head. , but not as a mandatory requirement.
3.8 Surface quality of ingots
The surface quality of the ingot has a great impact on the subsequent processing.
Large defects such as cold partitions, cracks, holes, and sills on the surface may cause cracking or even breakage of the ingot, which will greatly affect the yield and product quality. Therefore, the standard specifies the surface quality of the ingot, emphasizing that “the ingot should be delivered on the machined surface”, which stipulates the surface quality requirements of the side and end faces of the ingot. At the same time, it is stipulated that the surface roughness of all machined ingots should be no more than 12.7μm.
3.9 Packaging, transportation and storage of ingots
This standard gives three specific ways to choose the packaging of the ingot, and also indicates that other packaging methods can also be used. There are also reasonable regulations for marking, transportation and storage. In order to facilitate transportation and packaging, and to ensure the safety of transportation, the standard provides an appendix. The ingot packaging with long distance and large specification can be selected by the wooden pallet packaging method specified in the standard appendix. The steel tray packaging method can be implemented according to the provisions in the appendix of the standard to ensure the safety of personnel, equipment and materials during transportation and storage.
4. Outlook
From the statistical results, after nearly 10 years of rapid development, the phenomenon of large capacity surplus of domestic titanium and titanium alloy ingots has gradually emerged. This phenomenon will likely lead domestic titanium processing enterprises to gradually reduce or only maintain the production investment of existing titanium and titanium alloy ingots, in order to purchase finished ingots to meet the demand for processed materials production, thereby promoting specialized ingot production enterprises. Formation and development. Formulating national standards for titanium and titanium alloy ingots and establishing reasonable testing items and indicators will not only promote the quality control and improvement of titanium and titanium alloy ingots, but also effectively guide the purchase of the demand side, the production of the supplier, and promote production. The standardization of transactions will improve the current state of non-standards in the domestic titanium and titanium alloy ingot trading, thus effectively promoting the healthy and sustainable development of China's titanium industry.
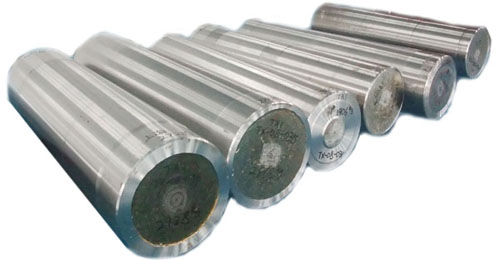
Attn : Jason
Email: jasontitanium@163.com
Sk