Preparation process of ultrafine crystal biomedical titanium alloy
Biomedical titanium alloy has high strength, good corrosion resistance, low modulus of elasticity, and excellent biocompatibility. It has become the main material of surgical implants and orthopedic devices. Ultrafine grain medical titanium alloys have higher strength and better fatigue properties and corrosion resistance than coarse-grain medical titanium alloys. Moreover, ultrafine-grained titanium alloy can induce bone tissue ingrowth, increase interfacial bonding strength, and accelerate bone repair process, and has broad application prospects in the field of hard tissue repair materials.
Studies have shown that the large plastic deformation technology is an important process for obtaining ultra-fine grain titanium alloy. The large plastic deformation technique can introduce high-density dislocations by applying a large shear stress without changing the size of the metal material, and refine the grain size to less than 1 micron to obtain an ultra-fine equimolar crystal. Fine grained material. This method is not easy to introduce impurities during the processing, and there is no residual shrinkage hole in the prepared sample, which avoids the problems of voids and poor compactness of the ultrafine grained materials prepared by other methods. At present, as a method for efficiently preparing ultrafine crystals and nanocrystalline materials, the large plastic deformation technology has been applied to the preparation of ultrafine crystal biomedical titanium alloy materials, and the comprehensive properties of the materials are optimized by grain refinement, including Strength, plasticity, fatigue properties, and corrosion resistance.
1, equal-diameter angular extrusion (ECAP). The technique is to place the sample into two or more equal-diameter curved passages which are mutually angled, and the specimen is subjected to uniform pure shear deformation through the passage under the action of pressure. Since the three-dimensional size of the sample before and after the extrusion remains unchanged, the effect variable can be increased by repeated extrusion, thereby obtaining a uniform and fine structure. For example, the grain size of Ti-6Al-4V after 4 passes of ECAP is reduced from 28 μm to 250 nm with a mold with an internal angle of 120°, and the tensile strength and microhardness are increased to 773 MPa and 2486 MPa (HV). ).
2, the high pressure torsion method (HPT). This method is the strongest grain refining ability in the large plastic deformation technology. The sample is subjected to a large pressure between the punch and the holder, and at the same time, the sample is subjected to axial compression and tangential shear deformation due to the rotation of the mold holder. The method can refine the grains and effectively close the internal pores of the material to improve the strength and toughness of the material. For example, the Ti-6Al-7Nb alloy was treated by the HPT method, and the microhardness value was increased by 78.70% after 5 turns. The strength of the ultrafine grained material prepared by the HPT method can be about 500 MPa higher than the ECAP method. Therefore, HPT technology is a very promising process for the preparation of ultra-fine crystalline medical titanium alloys.
3, the cumulative stack rolling method (ARB). In the process, two pre-surface treated thin plate materials are rolled and rolled at a predetermined temperature, and the same process is repeated and repeatedly rolled until the desired effect variable is achieved, so that the material structure is obtained. Refine. For example, after four cycles of rolling the Ti-25Nb-3Zr-3Mo-2Sn alloy by ARB method, the grain refinement, the tensile strength is increased by 70% compared with the original alloy, reaching 1220 MPa, and the yield strength is increased to 946 MPa. .
4, friction stir processing (FSP). This is a continuous, purely mechanical solid-phase welding process. During the welding process, the mixing head rotates at a high speed and the mixing needle is squeezed into the joint of the two butt plates. The shear friction heat generated by the rotation will surround the stirring needle. The metal becomes soft and then plasticized, causing plastic of the material at the processing site. For example, Ti-6Al-4V is treated by the FSP method, and the yield strength and tensile strength of the obtained alloy are 1067 MPa and 1156 MPa, respectively, and the elongation is still 21.7%.
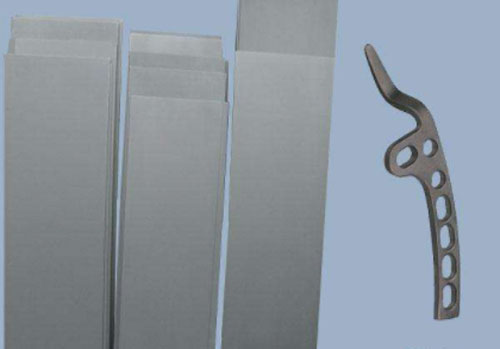
Attn : Jason
Email: jasontitanium@163.com
Skype: txcanberra